近几年来。国家对公路、铁路等基建的投入日益加大,迫切需要大量的砂石。然而有限的天然砂资源已经不能满足持续发展的需要。因此机制砂市场越来越大。机制砂市场的不断增长.带动了制砂设备的需求,特别是制砂用的立轴冲击式破碎机成为市场的热点。
转子是立轴冲击式破碎机的主要工作部件,而主抛料头是转子中损坏最为严重的部件,其状况如何不仅决定着破碎机的生产质量和效率。而且直接影响破碎机的可靠 性、使用寿命和成本的首要因素。资料显示,在我国目前所应用的立轴冲击式破碎机中,强度本身已经不是影响其寿命的主要问题,最关键的问题是主抛料头的磨损 e1],而主抛料头的磨损首先与抛料头所受的载荷有关,所以对抛料头的载荷研究是至关重要的。

1破碎机的工作原理
立轴冲击式破碎机主要由转子、破碎腔、传动机构和机架构成,其中转子是立轴冲击式破碎机的 主要工作部件,如图1所示。物料由人料口进入破碎机,转子在电机的带动下高速转动(转速一般为1400—1800r/min),矿石靠转子表面摩擦力和导 向板等的作用随转子转动.同时受离心力的作用向外抛射,当离开转子时与主抛料头发生碰撞,矿石以几乎达到了转子边缘的线速度向外抛射.冲击于破碎腔壁和分 料器四周自由落下的一部分物料上发生粉碎,被破碎的物料由下部排料口排出,和循环筛分系统形成闭路,经多次循环.达到所要求的产品粒度。

立轴冲击式破碎机的主要破碎形式就是击碎。经过加速的石块.在抛料头的碰撞下。一部分与破碎腔发生碰撞破碎.一部分与石块发生破碎,主抛料头在石块长时间 的冲击下磨损非常严重.经过一段时间后就必须更换.不然不但会影响破碎效果还会影响到转子本体,转子本体的磨损会影响其动平衡,容易造成主轴断裂等不良后 果,而更换一次立轴冲击式破碎机的抛料头需要0.3—0.5万元,造成很大的浪费。主抛料头的磨损主要是受到冲击以后所产生的冲击磨损(磨损后的抛料头如 图2a所示),每一组抛料头是有9个组成,从实际工况看,每次都是中间的3个磨损最为严重,为了不影响转子的动平衡,每次更换都是全部更换造成很大的浪 费,这时候就需要研究主抛料头所受的载荷,以达到延长抛料头的寿命的目的,但是试验机不能很好地模拟立轴冲击式破碎机的真实工矿,现实试验又太费时费力, 虚拟样机技术是很好解决这个问题的方法,而adams为实现虚拟样机提供了很好的平台。
2 破碎机转子建模
立轴冲击式破碎机转子(以山特维克生产的rp109)主要由转子本体、主抛料头、副抛料头、耐磨夹板、上耐磨板、下耐磨板、分料锥、定位块、挡料板等 180多个零件构成。在转子本体的内侧有6块挡料板,这种结构使得转子在加速物料的同时形成死料区以减少自身磨损,配合一定范围的转速,使物料的破碎过程 发生在转子外部由物料自动形成的冲击在转子中。主抛料头的作用是导向。通过转子对石块的加速,在转子内部形成涡流状,通过主抛料头的导向作用,使石块改变 方向沿着转子的切线方向向外抛射,这样就注定了主抛料头的主要失效形式为冲击磨损,因此需要对主抛料头的材料进行特殊处理,来增加主抛料头的耐磨性。
显然,对应于破碎机的正常工作状态,建模时,应当按照物料在转子内部形成料层以后的实际形状进行简化。简化后的转子模型内部呈圆柱状,物料与转子的接触由 石子与金属的接触变为石子与石子的接触。而且,石料被转子加速后更容易抛出,这样除主抛料头外其余的零部件都与转子合为一体,以此来模拟主抛料头的实际工 作过程。以solid works为工具进行建模,并将solidworks文件另存为parasolid格式导入adams中。导入的模型如图2b所示。
3 设定模型的参数及约束条件
材料的设定:因为简化后的转子模型内部呈圆柱状,物料与转子的接触由石子与金属的接触变为石子与石子的接触,所以设定简化后转子本体的内侧材料为石灰石。 由于在adams没有默认的石灰石属性,所以将转子内侧的属性设定为:弹性模量4.1e+010n/m ,密度为1500kg/m3,洎松比为0.3,来模拟石灰石的属性,设定转子本体的外侧材料为钢,弹性模量设为:2.07e+01 1n/m ,密度为:7801kg/in。,泊松比设为0.29:主抛料头的属性设置同转子本体的外侧材料。在adams中转子的人料口处加入物料,在实际工况中, 需要破碎的物料一般为不规则形状的石灰石,入料粒度是小于55mm,故本文中添加简化尺寸为边长20mm到50ram不等的立方体.设定属性亦为石灰石属 性。
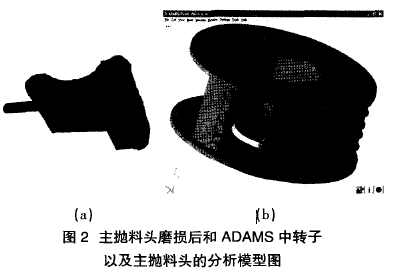
旋转参数设定:在模型和大地之间加一个铰链,在铰链上设置—个旋转运动,旋转方向为逆时针,转速分别设为1400r/min、1450r/min、 1500r/min、1600r/min、1700r/min,1750r/min、1780r/min和1800r/min,据此来模拟物料经过不同加 速后在离心力和摩擦力的作用下.经过主抛料头的碰撞后被抛出的过程。石块对转子本体的冲击力在另外的文章中另有叙述。添加约束和接触:在转子本体的内侧 (材料为石灰石)和外侧(材料为钢)以及主抛料头(材料为钢)两两之间加上锁定,使它们在运动中成为一体。在每一个物料上添加和转子本体以及主抛料头的实 体对实体接触.接触力设为碰撞,刚度设为1.0e+008n/ram,阻尼比设为1.0e+004,穿透深度设为1.0e一004ram,摩擦力的设置按 照库仑摩擦设置,静摩擦系数设为0.3,动摩擦系数设为o.1,其余的按照adamds的默认设置[引。仿真:时间为1.5s,steps为5000。确 定这些参数的基本原则是,在保证石料全部被抛出的前提下.尽量节约时间并能提高仿真精度。
4 仿真结果
利用adams软件并按照前述的模型参数级约束设定,可以得到转速为1400 r/min、1500r/min、1600 r/min、1700r/min和1800r/min时主抛料头的总体受冲击力情况,如图3所示。图3中,每一次碰撞在图中表现为一次峰值。可以看出,转 子在1400r/min时,石块加速均匀.碰撞次数最多,在1.4454s时石料被全部抛出:160or/min和1700r/min时所受冲击力相对比 较平稳,受的平均冲击力(每次冲击力之和除以受冲击的次数)也相差不大,石料分别在1.33s和1.31s被全部抛出;在1800r/rain时,碰撞次 数最少。这可能是由于转速的增大,石料未经过充分碰撞就被强大的离心力抛出转子;虽然最大冲击力和平均冲击力是最大的,但是除了最大值外其余的冲击力都比 前几个转速的小。从图3可以看出,在1800rpm时石料被全部抛出的时间只有1.25s,显然,石料未经过充分的碰撞加速就被甩出转子,对其破碎效果会 有不利影响。这说明,破碎效果不总是随着转速的提高而变好.而且最大冲击力和平均冲击力很大还会加速主抛料头磨损,长时间的冲击磨损会使主抛料头的寿命大 大缩短,进而对转子本体的动平衡造成很大的影响。因此,合理地选择转速对于增加主抛料头的寿命和提高破碎效率非常重要。通过adams对仿真的后处理,得 到主抛料头的最大冲击力和平均冲击力随主轴转速变化的数值曲线.如图4所示。由图4看出,最大冲击力在转速1500—160or/min以及1750— 1780r/min时相对增幅较大.在1400—1500r/min和1600—1750r/min时相对较平稳,而平均冲击力在1400— 1450r/min和1650—1750r/min时相对增幅较大,在1450—1650r/min时相对较平稳。由于物料是立方体的,是平面还是尖面与 主抛料头接触所产生的冲击力是不同的,在最大和平均冲击力突然变化的转速区间,尖面与主抛料头的碰撞的几率很大,加剧了主抛料头的磨损,从而影响更换主抛 料头的频率。造成很大的浪费。由图可以看出。最大冲击力比平均冲击力高两个数量级.即物料对主抛料头的瞬间冲击力很大。由此可以知道,1400— 1500r/min以及1600—1750r/min是主抛料头受力均衡,转子能获得平稳运转的转速区间:降低最大冲击力的值和频率非常必要,这既与转子 结构及相关参数的优化有关,还要分析进料粒度均匀性的影响和石块与主抛料头碰撞的主要区域。
转速是影响立轴冲击破碎机破碎质量、效率以及寿命的重要因素,但破碎效果不总是随着转速的提高而提高.高转速还会加剧主抛料头的磨损,严重影响破碎机的使 用寿命。仿真分析表明,1400—1500r/min以及1600—1750r/min是主抛料头受力均衡,转子能获得平稳运转的转速区间;此外,为了全 面兼顾破碎机的破碎质量、效率以及使用寿命,降低最大冲击力的值和频率是至关重要的,因此既需要考虑转子结构及相关参数的优化,还要分析进料粒度均匀性的 影响。对于石块和主抛料头的主要碰撞区域的确定也是非常重要的,值得进一步研究。
转载请注明出处,上海巍立路桥设备有限公司http://www.shwlm.com/news/hy/695.html